One Small Step for a Plant, One Giant Leap for Energy Efficiency at GM
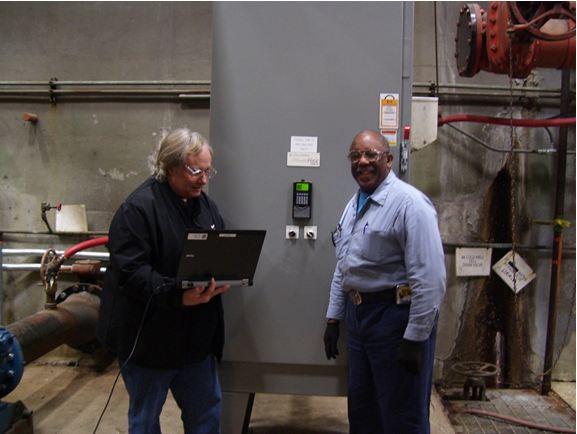
Worldwide, GM is dedicated to energy efficiency and is working toward a goal to reduce energy intensity from its facilities by 20 percent by 2020. One of those facilities is Saginaw Metal Casting Operations (SMCO).
Last year, SMCO installed new equipment that saved 3,650,000 kilowatt-hours of electricity per year. That’s enough energy to power over 380 homes for one year.
Working with the plant’s maintenance team, Project Engineer Ron Pokrak replaced SMCO’s fixed speed water pumps with variable speed pumps. You see, manufacturing facilities use water to cool equipment and for various processes we undertake as we build the world’s best vehicles. Pokrak’s team installed the new pumps on two of SMCO’s systems: the cooling tower and the water recycling system (reducing water use is also a part of GM’s manufacturing commitments).
However, running all these processes simultaneously requires a lot of water pressure, which can use a lot of energy. The fixed speed water pumps pump the same amount of water around the plant regardless of how much water was needed at any given moment. The variable pumps, however, continually look at the water pressure and adjust accordingly. When one piece of equipment is turned on, the pump speeds up to keep water pressure at its needed level. When a piece of equipment is turned off, the pump slows down, saving energy.
“What we did was replace a Clydesdale with a race horse,” Pokrak said. “The nice thing about the savings is we needed to replace worn out equipment anyway. By standing back and rethinking the designs, it cost very little money to achieve the savings.”
A company’s energy efficiency also affects its bottom line.
Last year, the Saginaw central maintenance team reduced structural water pumping energy costs by more than $500,000. In addition, Consumers Energy provides rebates to facilities that install projects that reduce energy consumption. The Saginaw facility received a check for $61,400 as a result of its energy saving projects.
“This wasn’t done by one giant leap, but by many small steps toward a common goal encouraged by our plant leadership,” Ron said. “It is amazing what can be achieved by a diverse focused group working toward a shared vision. The biggest hurdle we face in 2013 is beating the benchmark we set for ourselves last year.”
SMCO is one of 54 GM facilities to meet the ENERGY STAR® Challenge for Industry, a U.S. Environmental Protection Agency initiative designed to improve the energy efficiency of America’s commercial and industrial buildings by 10 percent or more. The agency named GM one of its ENERGY STAR® Partners of the Year for energy management in 2012 and for sustained excellence in 2013, the highest recognition a corporation can receive.