When Opportunity Knocks
Miguel Cardenas, Senior Staff Engineer, Kohler, Wisconsin, U.S.A.
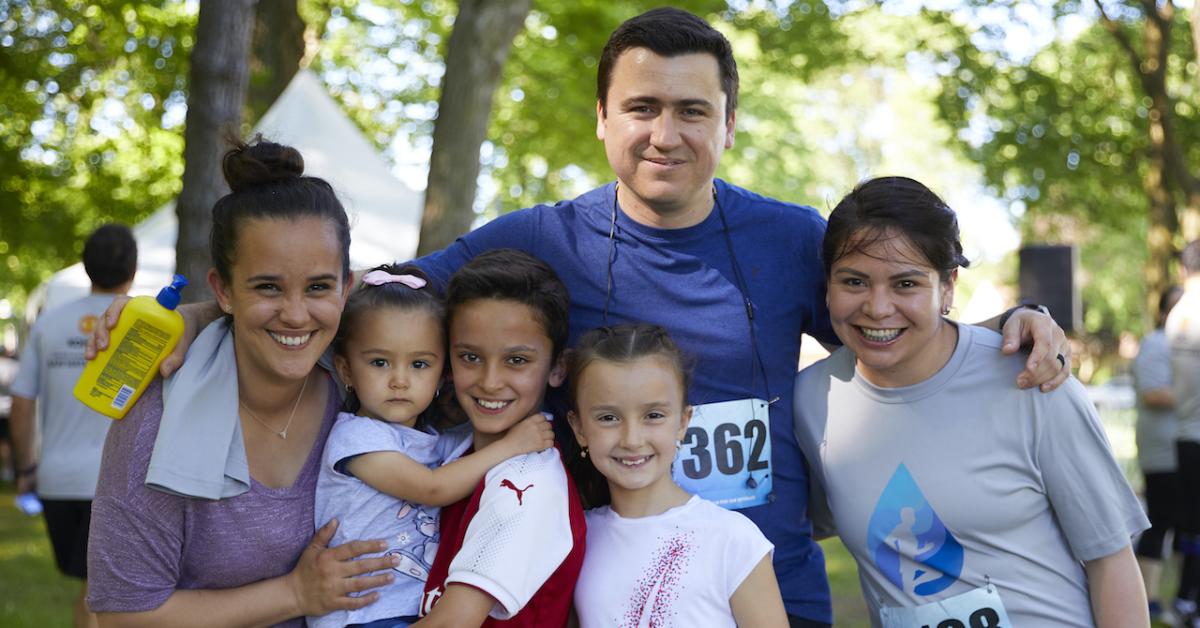
Miguel Cardenas had no plans to leave his job—let alone his home country. But when opportunity came knocking, he enthusiastically answered.
The engineer was happily working and living in Mexico with his family in 2016, when some of his colleagues made the move to Kohler Co. Even though Miguel was happy with his employer of 13 years, he was soon persuaded to also take a chance on Kohler.
“I wasn’t really looking for a change, but my former colleagues talked about the professional growth and company values Kohler offers, and I decided I couldn’t pass it up,” explained Miguel, who started in Kohler Engines and is now a senior staff quality engineer in Kitchen & Bath.
Miguel has an accomplished background in continuous improvement, an area where he’s quickly made an incredible impact at Kohler. He manages continuous improvement methodology, working across production, quality, materials, and manufacturing. His passion is nurturing a culture built on continuous improvement.
“It’s all about finding what doesn’t work for people and helping them figure out a better way to do it,” Miguel said. “Every small win is bigger than face value. It accumulates into a major improvement or possibility. It gives you time back in your day to invest in other projects.”
A huge area of impact for Miguel came in early 2020, at the beginning of the COVID-19 pandemic, when his cast iron team was asked to step outside their comfort zone.
“The company wanted to help our community health care workers, and one of their needs was face shields. We were asked if we had any capacity to help, and we jumped on the opportunity,” he said. They called in help from Kohler’s new product development, engineering, materials, and purchasing teams, and together, they figured out a way for the cast iron foundry to make plastic face shields.
And in true continuous improvement form, Miguel and his team kept fine-tuning to make a better process and product.
Once the process was perfected, they began to recruit more volunteers to increase face shield production. Miguel called upon his fellow members of the VIVA KOHLER business resource group—individuals from across the Latinx community—who stepped up to help. As the volunteer base grew, production eventually topped out at 1,200 face shields per day for area hospitals, fire departments, nursing homes, and clinics, making more than 60,000 in total over several weeks.
“Working in continuous improvement is always rewarding, but the meaningful impact of that project is something I’ll never forget—especially the way it brought our community together,” Miguel said. “It’s given us a renewed motivation to continue thinking outside the box and challenging ourselves in everything we do.”
By now it seems challenging himself is second nature for Miguel. From making an international move with a young family to transforming a cast iron foundry team into a face shield production operation, he faces those challenges head-on and is making a name for himself.
“It was a huge change coming from Mexico,” he admitted. “But the fact that Kohler invested time, effort, and resources to bring me from another country really confirms the company’s commitment to its people. It was definitely the right move for me.”