Multimodal Manufacturing—Avoid Challenges in the ATMP Marketplace
by Noel Maestre, PE, LEED AP SlateXpace Director, and Peter Walters, Director of ATMPs
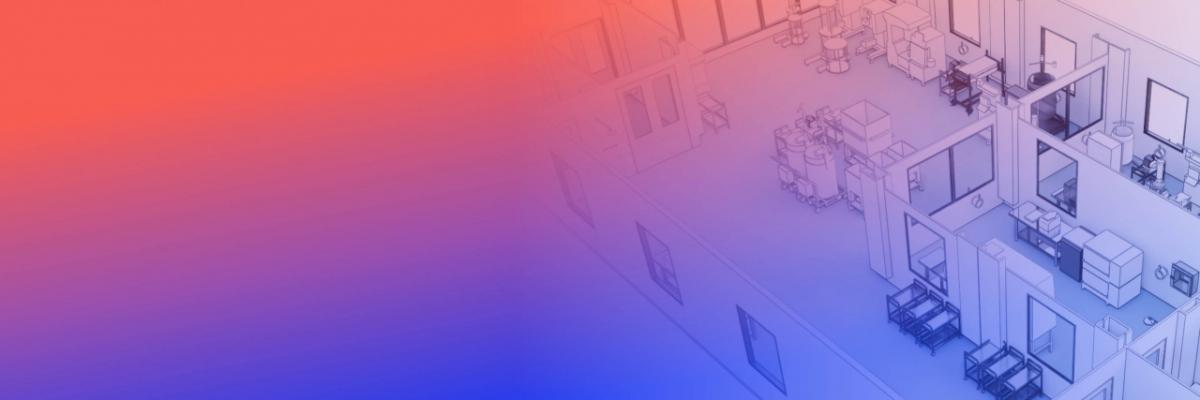
Facing pressure in the ATMP marketplace? Multimodal manufacturing is your solution for that.
Pharmaceutical developers have always been history-makers. In the 18th and 19th centuries, they gave us the world’s first vaccines. In the 1980s, they ushered in the golden age of recombinant therapeutic proteins. Today, they’ve brought us to the doorstep of advanced therapy medicinal product (ATMP) manufacturing, which is an idea that could transform how we approach the complex health needs of a global population.
But making history isn’t just about ideas. It’s about understanding the many challenges that lie between an idea and its real-world application, and finding reliable ways to overcome those challenges. For ATMP developers and manufacturers, those challenges very often spring from three core must-haves: quality, speed and a diverse portfolio. When all three are in alignment, amazing things can happen. When one is compromised—well, that’s where challenges arise.
A new solution is emerging to address those challenges and keep ATMP innovation moving: multimodal manufacturing facilities. These facilities are designed to balance the efficiencies of a standardized and modular cleanroom template with just enough configurability to suit unique operator needs. As a result, they’re becoming known as a modern, cost-effective, highly flexible solution to the present-day challenges and future needs of ATMP manufacturing.
A modular GMP suite accelerates speed-to-market
Challenge: Accelerate speed-to-market
The COVID-19 pandemic has highlighted the frailties of our current pharmaceutical industry. Heroic attempts to develop vaccines are well underway, but hundreds of thousands have died in the meantime. There’s a clear opportunity here to improve our industry’s responsiveness to unforeseen health threats.
Also, as much as speed is a matter of human life or death, it’s equally important to the survival of businesses. In the hugely competitive ATMP landscape, so much depends on getting to market first.
Solution: A modular GMP suite
First, its templated design makes it especially suitable for off-site fabrication, which translates to enormous time savings over traditional stick-built construction.
Once in place, such a suite eliminates traditional bottlenecks in the development and manufacturing process. That’s its second speed advantage: it streamlines regulatory approval (validate your manufacturing space once, then focus on licensing individual products) and makes product changeover a fast and simple process (decontaminate, swap equipment, and keep going).
A well-thought-out multimodal template standardizes just enough of the facility design to eliminate common bottlenecks
Challenge: Adapt to a rapidly evolving field
From weekly scientific breakthroughs to the constant evolution of manufacturing technology, keeping facilities, processes and product portfolios up-to-date is a constant challenge.
Solution: Reconfigurable templates
To maintain speed while responding to an industry that never stands still, ATMP manufacturers need facilities that are highly adaptable and reconfigurable. That’s where a well-thought-out multimodal template shines: it standardizes just enough of the facility design to eliminate common bottlenecks, yet preserves the flexibility needed for customization.
Built-in flexibility—there’s much less risk involved and a much higher probability of a return
Challenge: Protect capital investment
The tradition of investing heavily in a “dedicated facility” is no longer in line with today’s business reality. With so much competition and such high investor expectations, companies must instead develop diverse, complex pipelines that maximize the odds of reaching commercialization, if only for one product among many. Dedicated facilities, for all of their sophistication, simply aren’t designed to support such a degree of ongoing product diversity, which puts them at risk of early obsolescence.
Solution: Invest in a low risk, highly flexible facility
Today’s ATMP manufacturers need agile, reconfigurable GMP environments that can support multiproduct pipelines (covering both traditional biotech products like therapeutic proteins and vaccines, as well as novel ATMPs). This means that companies can invest in a facility without having to bet everything on a singular product; with so much built-in flexibility, there’s much less risk involved and a much higher probability of a return.
The “building block” nature of a multimodal GMP facility makes it especially suitable for flexible, needs-based expansion
Challenge: Commercialization
The ATMP industry faces a great unknown when it comes to commercial manufacturing. With fewer than ten approved products in the marketplace, there simply isn’t a template for scaling from clinical to commercial development. For the thousands of ATMP products currently in clinical trials and hoping for an eventual share of the commercial marketplace, this leaves many questions unanswered.
Solution: Flexibility to scale out
The “building block” nature of a multimodal GMP facility makes it especially suitable for flexible, needs-based expansion, giving companies control over if and how they scale to commercial manufacturing when the time comes. Because these “blocks” come in different sizes and feature different sets of functionalities, companies can start small and grow as required—in other words, they don’t need all the answers from the get-go in order to feel assured of a fast and nimble commercial scale-up.
Modular “platformed” facilities are easy to replicate, quick to deploy, and designed for streamlined regulatory approval and reliable output
Challenge: Geographic restraints
Because of the personalized nature of gene therapies and the skills required to work in this field, ATMP companies must think strategically about where to build or expand their operations. Pressure is on to go where the talent pool is most abundant, where the logistics are simplest, and where the need is greatest.
Solution: Templated, deployable facilities
Modular “platformed” facilities can relieve some of this pressure while opening the door to a broader, more strategic company presence in multiple locations, because these templated buildings are easy to replicate, quick to deploy, and designed for streamlined regulatory approval and reliable output. Companies can use this approach to take advantage of several emerging trends:
- Build near a major transport hub for easier, more cost-effective shipping logistics
- Build near urban centers known for their manufacturing talent
- Deploy in emerging markets
- Bolt a modular GMP suite onto a facility already providing patient point-of-care, such as a hospital, for direct delivery of personalized therapies
A modular, multimodal GMP facility is perfectly suited for deeper vertical integration
Challenge: Improve vertical integration
A turbulent supply chain has made many ATMP manufacturers anxious about the quality, reliability and cost of their critical raw materials, such as viral vectors or plasmids.
Bringing production of such materials in-house will afford these companies more control, but it does create challenges in terms of internal capabilities.
Solution: Pipeline control and adaptability
A modular, multimodal manufacturing facility is perfectly suited for deeper vertical integration. Its versatility offers improved control over a diverse and complex product pipeline while allowing companies to introduce the equipment they choose and make as-needed adaptations.
Minimize downtime when pivoting between products
Challenge: Meet shifting needs
For CMOs in the ATMP marketplace, agility matters; they need to support many different clients with diverse needs, timelines, platforms, product complexities, all from inside the same facility.
Agility matters for ATMP companies as well, though in a different way: they need to be fleet-footed enough to adapt in response to shifting demand. Consider all the companies currently concentrating on a COVID-19 vaccine, for example. In a year or two, they’ll need a new target to pursue, and they’ll want to use their existing facility to do it. That means planning for flexibility today in order to meet the unknown needs of tomorrow.
Solution: Versatility of a modular facility
For CMOs who want to offer a broad set of services, and for ATMP manufacturers who want to minimize downtime when pivoting between products, a highly versatile and modular GMP suite, designed to maximize product flexibility, is the answer.
Ability to “lock in” on a guaranteed cost even before initiating design
Challenge: Improve cost & scheduling control
Companies are under pressure to accomplish two seemingly opposing goals at once: on the one hand, they must improve their odds of reaching commercialization by expanding their product pipeline, and fast; on the other, they need to control their spending while their products are still at the investigational stage, without any certainty of which will succeed, if any. Balancing these objectives—ambitious development versus careful cost control—is a significant challenge in the ATMP industry.
Solution: Lock in on guaranteed cost
Among its many advantages, the ability to “lock in” on a guaranteed cost even before initiating design is one of the key benefits of investing in a templated, modular facility. This cost certainty accelerates corporate decision-making and ensures that company leadership is aligned on expectations throughout the life of the project or facility expansion.
We’re in an extraordinary period of innovation and disruption in the ATMP industry—a period that needs and deserves equally innovative and disruptive solutions, designed to support the growth and success of a new generation of medicines.