GM’s Energy Stars: Jim Divilbiss, Flint Assembly
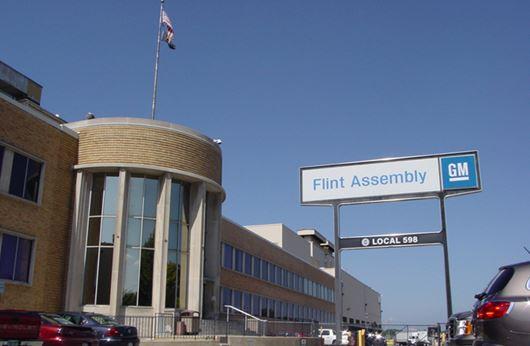
All this week, we will be recognizing GM employees from across the globe who helped the company achieve the U.S. ENERGY STAR Challenge for Industry earlier this year. Without their diligence and commitment to the goal, we wouldn’t be able to tout the fact that 63 plants across the globe have reduced 1.6 million metric tons of CO2 respectively.
Name: Jim Divilbiss
Title: Site Utility Manager
Facility: Flint Assembly
Length of time with GM: 18 years
1. What are some of the ways your facility cut energy intensity to meet the ENERGY STAR® Challenge for Industry?
We continuously work on core conservation areas such as compressed air reductions, improving shutdown levels when not in production, and reducing energy loads while running production. During this period we have also focused projects on installing high efficiency lighting, improving control and operations of the plants HVAC system, and steam usage reduction.
2. What are some tips you’ve picked up from your colleagues in the United States/internationally that you have incorporated into your facility’s energy savings program?
Our Mexico facilities have always been very aggressive in their energy and water conservation efforts. This effort shows in their energy metrics. After reviewing how they undergo shutdown procedures, we have been able to shut down various production equipment more efficiently. The projects that are reviewed during our monthly account meetings always provide us with some opportunities to evaluate our ability to implement new projects that other plants have already accomplished.
It’s always good to see that all plants are putting in the effort to reduce in all possible areas of their plants.
3. How do you engage employees to cut energy use in their day-to-day work?
We try to publish energy related stories in the plants newsletter which relate energy not just to work, but at home, as well. If the employees save money at home through energy efforts they will bring that back into the plant.
These stories also generate a lot of suggestions from the team that keeps them engaged in reducing energy at work.
Lastly, we try to recognize the plant publicly for their energy achievements which many times gets recognition in the local news.
4. What are some of the benefits you have seen at the plant since reducing energy usage by 13 percent?
The obvious benefit to the plant is reduction in cost to build vehicles. This makes us more competitive with other auto manufacturers. Also, when the local news reports about the plants achievements you see a since of pride in the employees in knowing we are doing the right things for the environment.
5. What are some energy savings tips that you take home with you at the end of your day?
The off switch is the most important energy-savings tool. Just like when I review our energy output at the plant, reviewing bills at home is vital to understanding where you can save money. Comfort is not free.