Top Recycling Technologies & Partners Supporting the Manufacturing Industry Today
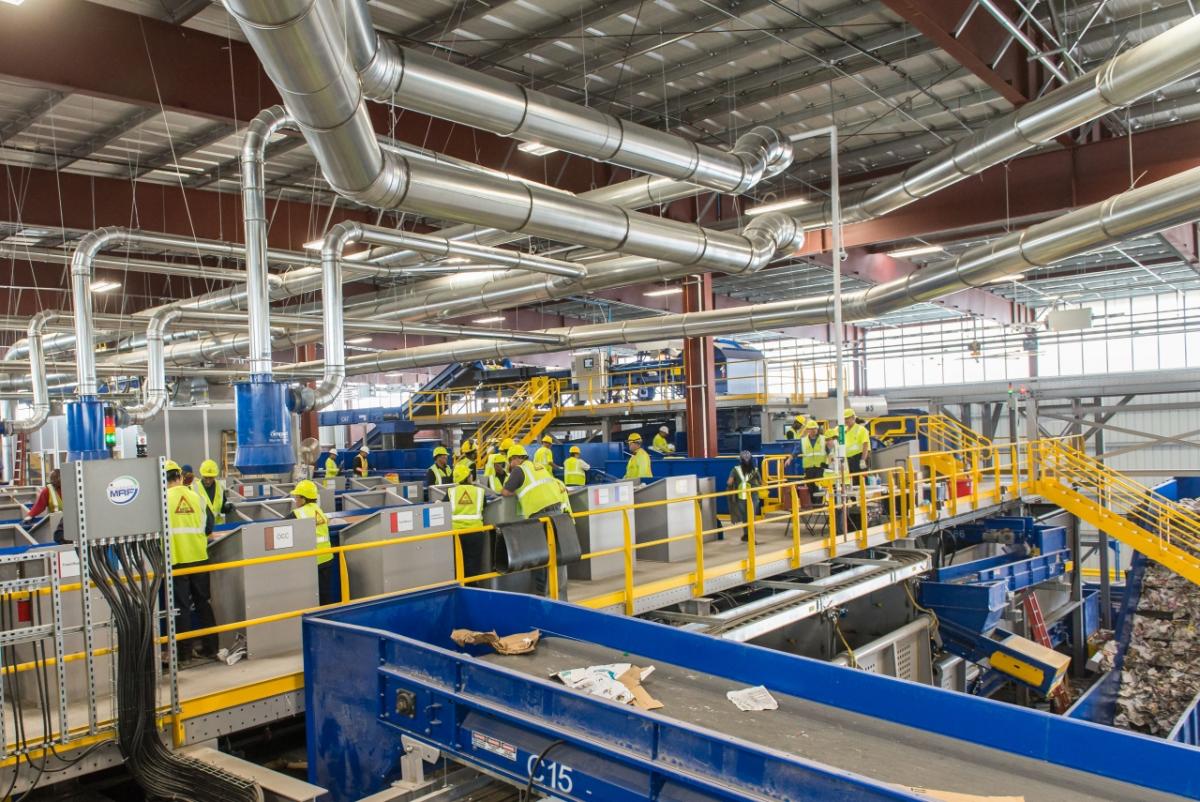
When businesses that involve manufacturing make recycling a priority, it can be more sustainable for the environment and have a positive impact on the bottom line. A 2020 study by the National Retail Federation and IBM found nearly 70% of consumers in the U.S. and Canada think it’s important for brands to be eco-friendly or sustainable. The manufacturing process plays a big part.
One way businesses can improve their sustainability quotient is by diverting more materials away from landfills and toward recycling operations. Another way is to use recycled materials in the manufacturing process.
There are constantly evolving demands for various materials your plant could be recycling. For example, as Republic Services reported in December 2020, recycled cardboard, boxes and packaging materials have been in recent demand due to increases in e-commerce and the demand for everyday products. However, recycling isn’t always an obvious or viable choice for manufacturing plants. Some challenges manufacturing plants might face regarding recycling include:
- Lack of recycling options nearby
- Lack of resources to manage recycling collection and processes
- Higher expenses to separate and recycle materials
- Lack of space for recycling collection
While there are some challenges, recycling in manufacturing continues to evolve and has come a long way in recent years. New technologies provide companies with more ways to recycle, and since consumers are increasingly ecologically minded, companies that embrace sustainability and improve their recycling efforts could offset recycling costs by improving customer sentiment and, thus, sales.
There are also potential immediate financial benefits to recycling, such as rebates for various materials. If you’re considering improving your recycling efforts in manufacturing or want to create a recycling program from scratch, consider these recycling technologies and partners that can help.
Republic Services
Republic Services is working on innovating recycling technology for businesses that use manufacturing plants to produce products. For example, their “Next-Gen” recycling facility and learning center in Plano, Texas, uses advanced sorting technologies to separate material in milliseconds and processes 350 tons of recyclable material per day. The plant’s technology includes:
- Optical sorters
- Next-generation anti-wrap fiber screens
- Automated, touch screen control systems
- Tablet-based capabilities for real-time systems management, remote access and data acquisition
Republic Services recycling plants are available throughout the country to help manufacturing facilities divert more waste into recycling and earn potential rebates that can provide financial savings. They also partner with recycling plants across the country to make recycling available to more manufacturers.
Republic Services customers receive a dedicated account executive to help optimize recycling and waste management, save money, avoid downtime and help keep employees safe through robust waste compliance standards. To learn more about Republic Services manufacturing and industrial waste services, visit RepublicServices.com.
TerraCycle
TerraCycle also provides industrial waste solutions, where manufacturing facilities around the globe can recycle large amounts of difficult-to-recycle waste, as well as small, atypical waste streams, like personal protective equipment.
They offer several loading methods for materials, including live loading at a plant and having TerraCycle pick up the material; a drop trailer delivered by TerraCycle that you’d load materials into; or delivery of materials from a plant to TerraCycle.
Closed-Loop Manufacturing
You may be familiar with closed-loop manufacturing if you’ve heard the term “up-cycling.” Closed-loop manufacturing is using material waste and recycled products to create new materials, which may then possibly be recycled again and again. Instead of sending waste to a landfill, closed-loop manufacturing processes give that waste a valuable purpose.
Companies from Nike to Apple aspire to be fully closed-loop manufacturers in the near-future. Even semi-closed-loop companies can increase the amount they’re reusing and decrease their environmental footprint.
When companies use material waste and recycled materials to create new products, they can share those efforts with consumers and boost their sustainability profile. Ultimately, reusing materials also cuts down on manufacturing costs, including having to source or create new materials for products.
Advanced Recycling / Mixed Plastics Recycling
Advanced recycling, also called chemical recycling, is a process of changing the chemical structure of plastic waste like composite and laminated plastics and plastic films. Through this process, the plastics can be used for new purposes. For example, by converting plastic properties into shorter molecules, the plastic waste can be used to produce:
- Virgin plastics
- Synthesis gas
- Liquid and semi-liquid products
- Petrochemicals and fuels
- Industrial waxes
When they’re not recycled, “hard to recycle” plastics may be exported, buried or incinerated. To avoid this, manufacturers may adopt advanced recycling methods for their plastic waste.
One England-based company called Recycling Technologies converts plastic waste into a wax/oil product that can be used to produce new wax and plastic products. British grocery chain Tesco partnered with Recycling Technologies to divert soft plastic waste from the landfill and into recyclable materials. Today, Tesco has soft plastic collection points throughout its chain of stores. The plastic will be recycled into new packaging.
Here in the U.S., Hefty launched its EnergyBag program, which diverts non-recyclable plastic items from landfills. Consumers can place these plastics in special orange bags that are sent to energy conversion facilities.
Manufacturing plants that produce hard-to-recycle plastic waste can look into advanced, or chemical recycling options. One company to watch is PureCycle Technologies, developed by Procter & Gamble. The PureCycle Technologies process separates contaminants, color and odor from plastic waste feedstock so it can be transformed into recycled polypropylene (PP). This polymer plastic can be used to create products like packaging, reusable containers, automotive components and laboratory equipment.