The Latest Advancement in Commercial Construction Is … Wood
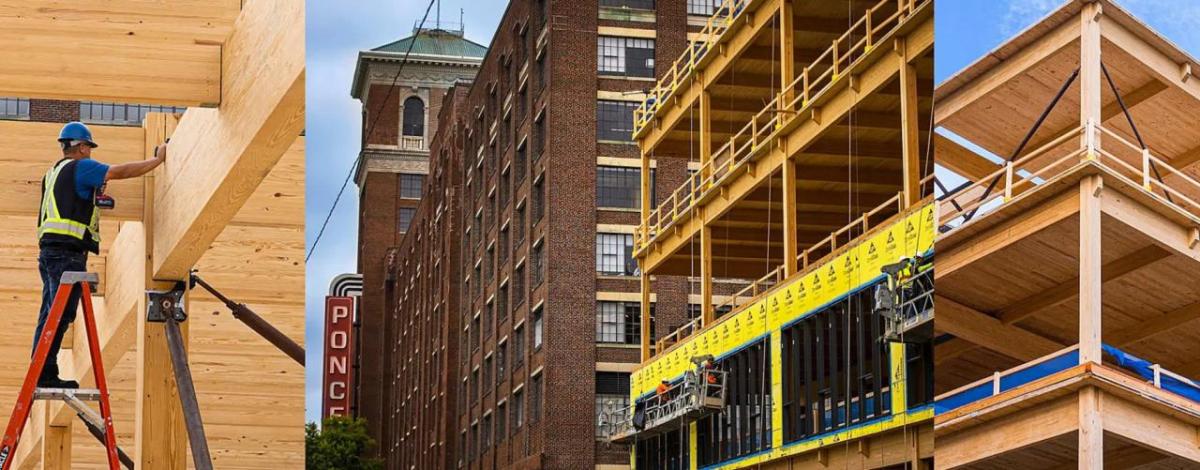
The unique wood structure of 619 Ponce in downtown Atlanta is the result of collaboration with customers on their unmet needs, innovative thinking and a focus on long-term value creation. When completed, it will be the largest mass timber building made from southern yellow pine and showcase the benefits of challenging traditional construction methods.
The building at 619 Ponce in downtown Atlanta is no ordinary building. It stands out from its concrete and steel counterparts because its columns, beams and floors are crafted from large pieces of glued-together wood known as mass timber.
Driven by a partnership between Georgia-Pacific, Jamestown, a global real estate investment and management firm, and SmartLam North America, 619 Ponce aims to demonstrate the viability of using mass timber in large-scale construction and give a real-world example of how it reduces construction time, improves site safety and reduces carbon emissions compared to traditional concrete and steel buildings.
Mass timber is typically made from species of wood that are imported from Europe or Canada, but Jamestown wanted to use materials sourced a little closer to where the building was being constructed. It chose to use southern yellow pine, a type of timber readily available in the southeastern United States, but that hadn’t really been extensively used in the manufacturing of mass timber. Anyone taking on the project would need to be willing to innovate and experiment.
“Most folks just say, ‘This is what we offer and don't ask for anything else,’” says Derek Ratchford, CEO of SmartLam North America. “They told me you're wanting vanilla ice cream mixed with chocolate and sprinkles on top. We do vanilla ice cream. If you want vanilla ice cream, call me.”
SmartLam takes the smaller pieces of lumber produced by companies like Georgia-Pacific and forms them into the mass timber beams and floors specified by a building’s architects and engineers. The process demands very specific quality requirements – wood that is about 5% drier than typical construction lumber and that is aesthetically pleasing with minimal flaws or knots.
“We've gone through this with a lot of folks that just say, you know what? It's too much trouble. We're not interested,” Derek says. “But Georgia-Pacific didn’t shut the door on the idea.”
Fritz Mason, president of Georgia-Pacific’s lumber business, says that’s because the company saw the potential long-term value of developing the capabilities required to serve customers in this growing new market, even if that means disrupting the typical ways they operate.
“Not every producer is willing to invest the resources or has the capability to pursue that specialization,” Fritz says. “We’re trying to look for opportunities where we can profitably add value to what we produce for our customers.”
Recent investments in modernization and the construction of a state-of-the-art lumber mill in Albany, Georgia, he says, allowed Georgia-Pacific to gain a technological advantage and meet SmartLam’s requirements.
Georgia-Pacific also benefitted from having employees who embrace creative destruction – being willing to make changes on the fly and modify their processes.
“It forced us to go way outside of our comfort zone,” says Brian Garrett, kiln asset center owner at Georgia-Pacific. He oversees all of the drying operations at the company’s mills and helped lead the team on the 619 Ponce project.
He says they had to completely rethink their process from beginning to end. It was difficult, but ultimately, they proved they were able to safely provide a quality product that others couldn’t.
"It forced us to go way outside our comfort zone."
BRIAN GARRETT
Kiln Asset Center Owner, Georgia-Pacific
John Mulcahy, Georgia-Pacific’s vice president of stewardship, says constructing buildings using mass timber has many benefits. Because all the parts are manufactured off-site, they show up ready to be put in place. That means once the foundation is poured, a crew of 8 to 10 people can raise all the pieces into place like a giant version of a kid’s construction toy. This decreases construction time compared with traditional steel and concrete buildings and reduces the potential safety risks for workers on construction sites.
Mass timber buildings also have less embodied carbon – the carbon emissions arising from the extraction, manufacturing, transportation, construction and disposal of building materials – than concrete and steel buildings. About half the dry weight of wood is made up of carbon, which gets stored inside the building for its lifetime.
“Giving our customers an alternative that helps them meet their carbon goals is something we care about,” John says.
The last mass timber beam for 619 Ponce was placed in June of 2023. When it opens in 2024, the more than 100,000-square-foot building will house both offices and retail space, including Pottery Barn.
Fritz says Georgia-Pacific has learned a lot from the 619 Ponce project and that it’s proven to partners, such as SmartLam, the value it can bring to this growing market.
“GP just thinks a little differently,” SmartLam CEO Derek Ratchford says. “And I think that's what sets them apart as a supplier of choice.”