The Journey From Recovery to Circularity for the Tire Industry
Words by 3p Editors
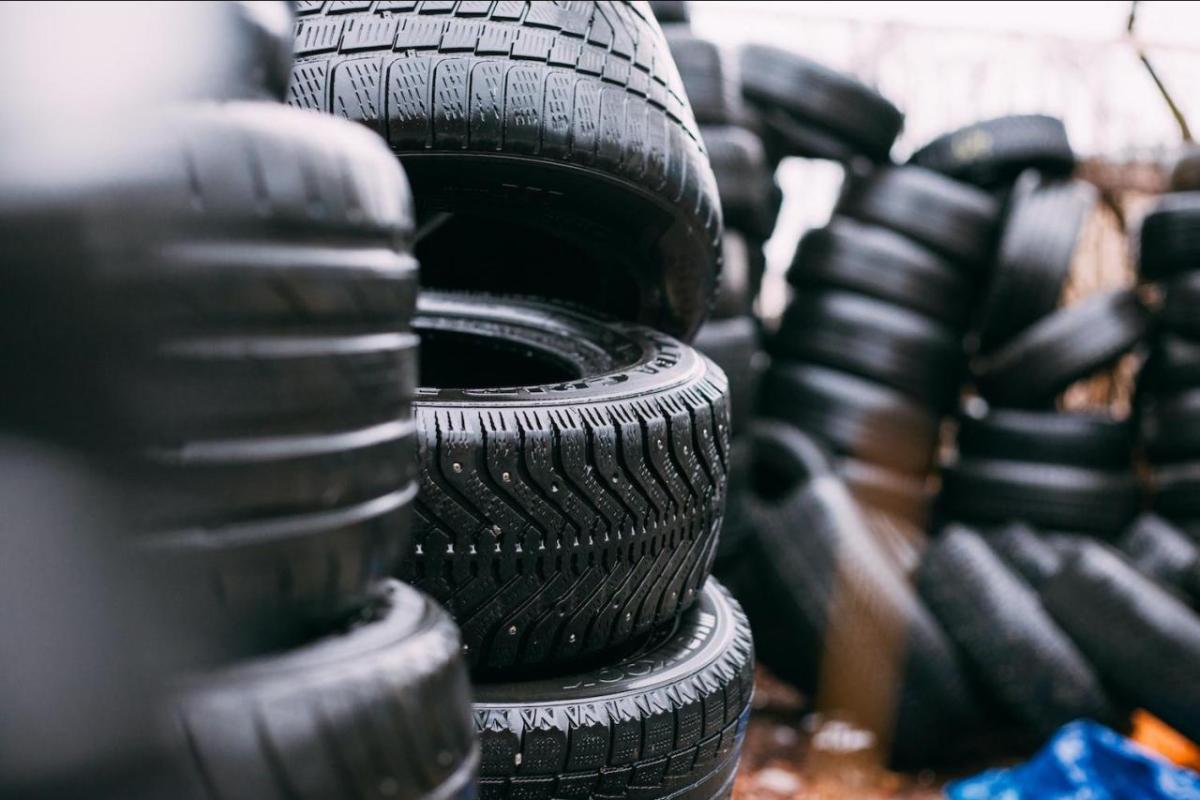
Originally published by TriplePundit
Heaps of scrap tires were once a common sight in countries around the world, whether stockpiled, taking up space in landfills or illegally dumped. But the picture has improved over the years, thanks in part to the growth of new markets for scrap rubber and other components of end-of-life tires (known as ELT). Countries including Brazil and India now recover almost all of the ELT they produce, and recovery rates exceed 90 percent on average across the European Union. The U.S. recovers around 80 percent of its ELT.
Still, ELT recovery rates rise and fall in accordance with demand and end markets for ELT materials. In the U.S., for example, the ELT recovery rate was 71 percent in 2021, compared to a high of 96 percent in 2013, according to data from the U.S. Tire Manufacturers Association (USTMA). The primary reason for this decline in the U.S. is that scrap tire recycling is not keeping pace with increasing annual generation. Other regions are faring better, with ELT recovery rates nearing 100 percent in Germany and France and hovering around 90 percent in Japan and South Korea.
New, more valuable use opportunities for ELT could provide even more incentives for ELT recycling and help further build circularity and sustainability into the tire lifecycle at the global level.
Moving toward a circular economy for end-of-life tires
Transitioning to a circular economy for ELT tires will require development of new markets for scrap tires. According to the U.S. Environmental Protection Agency (EPA) primary uses for ELTs include tire-derived fuel, civil engineering applications, such as sub-grade fill and embankments, and ground rubber applications including rubberized asphalts.
Tire-derived fuel — shredded or whole tires that can be burned for energy and for their material content — consume roughly 32 percent of annually generated ELTs in the U.S. Tire-derived fuel typically replaces traditional fossil fuels and decreases emissions of sulfur oxides (SOx) and nitrogen oxides (NOx). Further, the U.S. EPA recognizes the biogenic or natural rubber content in tire-derived fuel as carbon neutral, which reduces the carbon dioxide (CO2) emissions profile for this material. However, despite these benefits, USTMA’s Scrap Tire Management Summary report demonstrates that the use of tire-derived fuel in the U.S. continues to decline. This is in large part due to market dynamics including energy prices and demand.
Today, innovators are looking toward more sustainable ways to generate energy from ELTs. With next-generation carbon recycling technology in hand, emissions from tire-derived fuel could be captured and converted into new fuels, plastics, and other products.
Additionally, a process called tire pyrolysis — or thermal degradation of the organic components in tires at temperatures of over 900 degrees Fahrenheit (482 degrees Celsius) — produces oil, gas and recycled carbon black products in addition to the recovery of the steel. In Germany, Mercedes-Benz and other stakeholders are exploring the use of pyrolysis oil, produced in part from recycled tires, to make plastic car parts. Bridgestone is also working with partners in Japan to develop next-level recycling technology that can break ELT down to its molecular building blocks for reuse in products including synthetic rubber.
New technology can lead to new markets
Other traditional tire recovery uses could also see shifts in the near future. For example, a recent State of Knowledge Report completed by the University of Missouri and sponsored by The Ray and USTMA, finds promising economic, performance and environmental benefits from the use of ground ELTs in roadways. The report also identified data gaps including the need to better understand the benefits of rubber-modified asphalt relative to the issue of tire and road wear particles (tiny debris formed as the tire meets the road surface). USTMA is currently sponsoring research to answer this question through the University of Missouri, and the study is expected to be finalized later this year.
New recycling technology is opening the door to novel uses in the concrete industry, enabling planners to select applications where exposure to abrasion, fire, seepage, or other loss can be minimized or eliminated.
Though only small amounts of tire scrap have been added to concrete as a replacement for traditional material like gravel or crushed rock, that could soon change. A team of engineers from Australia’s RMIT University recently developed a compression-based process that can replace traditional concrete aggregate with tire-derived materials.
According to RMIT, the new rubber-based concrete meets Australian building codes. It is lighter than conventional concrete, raising the potential for reducing transportation and building costs.
Separate research from the University of South Australia also found ELT to be an economically viable and safe input for concrete in residential construction, further building curiosity around this potential end-life solution.
To inform developments like these, the Tire Industry Project (TIP) — a voluntary CEO-led sustainability collaboration under the umbrella of the World Business Council for Sustainable Development — outlines the relative contribution to circularity of different ELT-management pathways in its ELT management hierarchy.
Next-generation tire recycling and the circular economy
Getting to the next level of circularity will also involve new technology in the tire itself.
The use of bio-based materials in tires is one new approach. Michelin, for example, is focusing on bio-based alternatives for butadiene, a key ingredient in synthetic tire rubber, and Continental is looking to recycled rubber, rice husks and plastic bottles in its drive for sustainable materials for tire production. Goodyear’s commitment to using sustainable materials includes the use of rice ash silica, as well as the use of soybean oil, a surplus that is available beyond food applications.
In its Sustainable Development Goals (SDG) Roadmap for the tire sector, TIP raises additional opportunities for industry stakeholders to move toward circularity — which include scaling solutions to track and trace the flow of ELTs, fostering new or improved ELT markets, and developing standards and solutions companies can use to advance product design to achieve more sustainable outcomes.
“A systematic life cycle approach must be taken to achieve a circular economy, which can result in better environmental performance and improved security of supply of raw materials,” the Roadmap reads. “The design and manufacture of new tire solutions is a core area of competition between tire companies that seek to innovate new and proprietary performance attributes for their customers.”
The transportation sector, including the tire industry, has been at the forefront of the long, complex journey toward decarbonization and sustainability. And the movement from ELT recovery to circularity will help ensure that vehicle tires can come along for the ride.
Image credit: Robert Laursoo/Unsplash