Can Remanufacturing Build the Industrial-Sized Circular Economy?
by Susan Galer
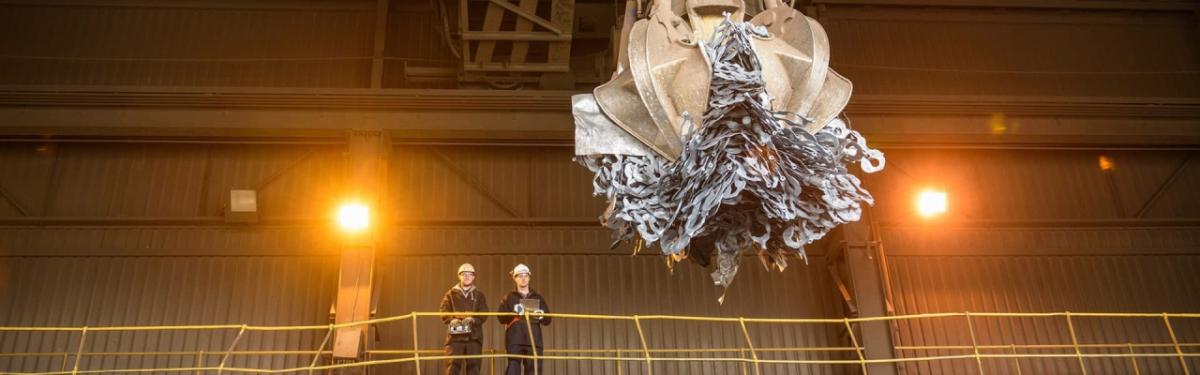
Consumer goods like clothing and bottled water dominate sustainability conversations, but the circular economy has to include the industrial manufacturers of the machines that churn out the products we use every day. We’re talking about the factories that manufacture the machinery and parts for farming tractors, construction excavators, robots, data centers, elevators, cars, wind turbines, heating and ventilation equipment, and more – essentially the infrastructure of modern, digital society. Closing the gap between sustainable aspirations and business realities is an industry-wide priority.
“Although remanufacturing has been an industry norm, the difference now is its direct connection to meeting sustainability objectives at scale,” said Georg Kube, global vice president and head of Industrial Manufacturing at SAP. “Organizations can gain faster near-term value from bringing back existing products and reusing them for innovations that help achieve net-zero and net-neutral goals across the supply chain.”
In a recent Oxford Economics study, respondents from industrial manufacturing and high tech industries said that results from their circular economy initiatives included better brand reputation (80%), increased innovation (79%), and enhanced regulatory compliance (78%).
Circular Economy Meets Sustainable Business Imperatives
Circular manufacturing has taken on new urgency. Material shortages are pushing costs higher. Easily disrupted supply chains add to challenges, where a single roadblock in one corner of the world cascades with massive negative impact on production elsewhere. At the same time, given increasing regulations, manufacturers have to calculate whether the energy consumption for one-time-use goods is profitable. Remanufacturing can help companies reduce the Greenhouse Gas Protocol Scope 1, 2, and especially 3 emissions that make up a significant percentage of carbon debt in their products. Localized remanufacturing is even more environmentally friendly.
“If manufacturers could harvest recyclable materials from locally sold and used consumer goods instead of dumping them in landfills, their customers become their suppliers for a fundamental change in supply chain dynamics,” said Kube. “Circular economy is a powerful way for manufacturers to demonstrate how they are committed to the environment and aligned with customers likelier to buy sustainably built products.”
Kube added that some organizations are generating a strong revenue stream from remanufacturing their own products and selling those same services to other companies. Manufacturers are also moving factories closer to remanufacturing locations, reducing emissions from shipping and logistics.
Remanufactured Supply Chains Coalesce Around Sustainability
For heavy equipment manufacturers that typically have large portfolios, the circular economy involves prioritizing which machines and components make sense to reuse based on actual product value and carbon emissions saved. Calculations include the cost of materials, components, and production, along with depreciation and lifetime energy usage. Manufacturers that buy back certain products from their distributors can disassemble the returned machines, clean up designated high-value parts, and upgrade the component’s capabilities for reuse in advanced releases.
“The goal isn’t to try and remanufacture every single product in your portfolio,” said Kube. “You want to remanufacture only those items with significant carbon savings and economic value, opening up possibilities for cost-effective innovation while complying with sustainability mandates and addressing customer expectations. Suppose you get back a second-generation pump. Its core has the highest value and most carbon emissions. You can take it apart and replace one chip in the motherboard to add a feature like remote control, transforming the product into the next generation.”
Business Sustainability Is Built on Data Sharing
Despite legal edicts and consumer-led clout, sustainable business practices deep in the industrial manufacturing supply chain aren’t a given. Once a manufacturer has decided which parts make the most sense for reuse, customers still need incentives to return the product; maybe the payment for returns exceeds the dumping costs. Managing the logistics to identify, inspect, and take back products will require trailblazing industry collaboration.
“As products are sorted between scrap and remanufacturing, the manufacturer needs accurate data that captures the flow of materials and financial information,” said Kube. “We are innovating with solutions like SAP S/4HANA, as well as business networks, to securely connect data within an organization and across trusted ecosystems. The circular economy will depend on a network of enterprises moving in sync towards a sustainable planet.”
Long before and after they touch our lives, products have a direct and indirect impact on the environment. Just reporting carbon emissions won’t make industries like farming, construction, energy, and automotive sustainable. Remanufacturing will tighten and shorten the loop between first-time product usage and reuse that reduces waste and increases profits, powering the circular economy.