Making Supply Chain Sustainability in the Chemical Industry More Efficient
By Dawn Rittenhouse
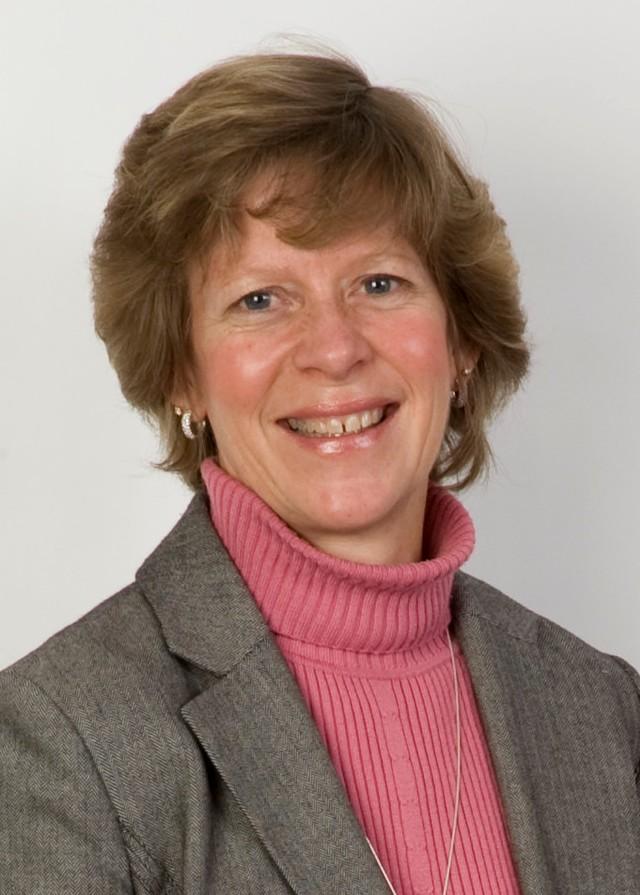
Adapted from comments delivered February 24th, 2016 at the GreenBiz conference in Phoenix
Companies participating in the UN Global Compact often point to their supply chains as one of the most challenging areas to improve their sustainability performance. This makes sense. For multinational corporations operating in multiple industries, supply chains aren’t chains at all. They’re webs --- vast, complex, and frequently shifting networks upon which the company relies to power its business. Despite the challenges, the supply chain cannot be ignored in any mature, well-integrated corporate sustainability strategy. In fact, the purchasing power of a company can significantly amplify any environmental and social change it might drive in its own operations. The trick for a successful sustainability supply chain strategy is efficiency, prioritization, and balance.
Early supply chain sustainability efforts, which often focused on having companies create their own supplier assessment processes, did not tick these boxes. Suppliers were forced to complete a battery of similar-but-different assessments and companies had to develop knowledge management systems to manage, analyze, and actually leverage the information they were receiving. Unsurprisingly, the result was inefficient, scattershot, and imbalanced.
That’s why DuPont recently became one of the first U.S.-based companies to join Together for Sustainability (TfS), an initiative to improve the sustainability practices within the supply chains of the global chemical industry. Recognizing that sustainability practices need to be included with price, quality and delivery information, , TfS was founded in 2011 as a procurement-led initiative that develops and implements a global program to assess, audit and improve supplier sustainability practices within its member companies. Sustainability information obtained via third-party supplier assessments and audits are made available to other TfS members. This simplifies and streamlines the process to extend sustainability principles into the supply chain for manufacturers and creates an easier process for suppliers, who no longer have to complete individual, duplicative forms.
For DuPont, such simplicity is vital. With a diverse portfolio of businesses, global footprint, and extensive operations, DuPont operates a highly complex, integrated supply chain. Of our estimated $10.2B sourcing and logistics spend in 2014, approximately 54% went to the top purchased energy and raw materials, 32% went to other purchased energy and raw materials, and 14% went to packaging and logistics. This spend is spread out across thousands – if not tens of thousands – of global suppliers, all of which rely on their own supplier network. However, not all of these suppliers are actually a sustainability risk. In fact, it’s likely that only a small percentage of suppliers pose such risk.
I like to think of this a little bit like the “80-20 rule”, with a little bit of a twist. Most companies probably purchase 80% of their raw materials from 20% of their suppliers. For those significant suppliers, the purchasing company likely has a decent handle on their operations and management practices. But, it’s the 80% of suppliers that are only supplying companies with 20% of their raw materials and goods that pose the most operating and sustainability risk.
This problem is one of the reasons the TfS approach is so useful. The sustainability information obtained via third-party supplier assessments and audits is collected consistently across different geographies and sectors. As a result, companies can access consistent, streamlined data to make the best decisions about their suppliers. TfS member companies can also provide access to consistent supplier training and recommendations on actions plans to improve sustainability performance. In turn, suppliers to the chemical industry benefit by only having to complete a single assessment that is then communicated to most of their industry customers. This strategy relies on the belief that competitive advantage is not achieved by how companies collect and manage supplier sustainability data but by how companies analyze and leverage that information to mitigate risk and affect change in their supply chains. This approach also leverages the strength of the chemical industry to drive improved supply chain performance, therefore supporting both individual company commitments as well as those embedded in other external commitments such as Responsible Care®.
Dawn Rittenhouse is the global Director of Sustainable Development for DuPont. She joined DuPont in 1980 and has held positions in Technical Service, Sales, Marketing, and Product Management. Since 1997, she has been working to integrate sustainability strategies into DuPont business units. She also leads DuPont’s efforts at the World Business Council for Sustainable Development (WBCSD) and the United Nations Global Compact.